Chapter 5: Single Minute Exchange of Die (SMED)
What is SMED?
Single minute exchange of die (SMED) focuses on reducing changeover and set up times, hopefully changeovers occur in less than one minute. It involves the conversion of internal set-up operations to external ones. It is very helpful to increase productivity (Moreira and Pais, 2011; Trout, 2022).
Importance of SMED to Lean
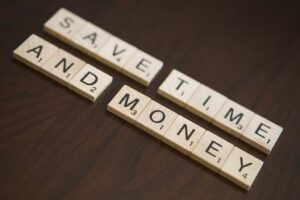
There are two main categories of improvement when implementing SMED: Human and Technical. The human element in manufacturing is improved through training and organization. The technical side of manufacturing is improved through engineering (Lean Production 2021). A quick change over is so important in lean manufacturing because it impacts the flow of production and takt time. Basically, the more time the process is delayed or stopped there is revenue lost and waste incurred (Trout, 2022). Consider these calculations to demonstrate the importance of SMED.
Takt time = Time spent producing each unit. With the known sales amount per unit, you can calculate the number of lost sales.
Lost Sales Revenue = Sales per unit x down time (seconds) / takt time in seconds
Example: A toy manufacturer sells action figures for $20 and can produce one unit per 60 seconds. Because their molds are all different, there is roughly 60 seconds of downtime per unit as it shifts from one type to another. So, the lost sales revenue would be calculated as: $20 X 60 seconds / 60 seconds. The toy manufacturer loses $20 (the cost of one unit!) every time they shift to a new mold. How could this process benefit from the use of SMED?
Here is a short, real-life example how SMED processed reduced internal set-up times 46% and increased production quality by 2% per day: The effectiveness of single minute exchange of dies for lean changeover process in printing industry (Indrawati et al., 2018).
How SMED Works
SMED works by shifting internal operations to external operations. Internal operations cause machine downtime, while external operations allow machines to continue to run. For example, at Toyota, a 1000-ton press changeover was improved by SMED, cutting changover time from four hours to only three minutes.
The process is simple and the benefits are huge (Diaz-Reza et al., 2017; Trout; 2022).
- List all current set up steps and time required (a table is very helpful for this!)
- Categorize the steps as internal or external.
- Convert internal to external
- Reduce internal set-up time
- Reduce external set-up time
- Standardize this work and measure set-up.
- Investigate the elimination of set-up.
Standardized work requires a few things in order to be successful. Takt time is used, to calculate the amount of demand from the customer. The work sequence must be identified and followed, including any changeovers. And finally, WIP and finished good inventories must visually demonstrated with kanban, to make sure no wasteful practices are used in the work.
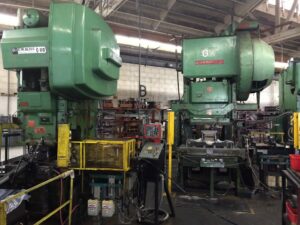
So consider some of these challenges below and how these could be improved through the use of SMED. Here are specific challenges, typical for metal-stamping press:
- All dies are different sizes and heights.
- Every die needs a different press shut height.
- Dies are held in with long threaded bolts often having stripped threads an badly worn or damaged heads.
- Tools, nuts, and bolts needed for changeover are missing.
- Operator is unable to locate the required tool or die.
- Taking the old die out and/or putting the new die in the machine is at least a two-person job.
- Wasted motion and time.
- Nothing is standardized.
- About 20 to 50% of the time is spent in adjusting and 10% of the time in locating and securing the new tools and dies.
SMED Best Practices
Below are some best practices and recommendations regarding the implementation of SMED (Lean Production, 2021).
Staged Tooling and Fixtures:
- If a part or tool must be placed into a fixture prior to an operation, such as machining, add a fixture so that while one part or tool is in the machine, the second can be set up in the fixture
Operations Conducted in Parallel:
- Which is faster? Complete all at once or one at a time?
Standardized Tools and Hardware:
- Consider how long it takes for a pit crew to change tires if the replacement tire had a different lug nut configuration.
- Standardized attachment points and methods reduce confusion and the number of fasteners, saving time.
- Standardization also applies to tool storage organization so that tools can be quickly located.
Quick Attachments:
- Clamps, cams devices, and u-shaped washers are used for quick attachments
- Pre-tightened bolts during external set-up, only need one final turn to provide clamping force during internal set-up.
No-Adjust Tooling:
- Locating pins, guides, and fixtures to eliminate adjustment
Assisted Tool Movement:
- Large dies or heavy tools can be moved with dedicated die carts, roller tables, or small conveyors than with forklifts or cranes.
- Mechanized tool change equipment allows pre-staging of the replacement tool and may also facilitate changeovers by the base equipment operator without additional indirect labor.
Challenges with SMED
There are a few general obstacles that organizations using SMED may face (Trout, 2022):
- Machine causing a bottleneck
- Costly jobs
- Missed or expedited deliveries
- Job or machine targeted for reduced order sizes
And finally: continuous improvement is important. What can be improved in other set-ups? What other set ups need SMED? Can checklists be created for SMED?
Real-Life Example: The Pit Stop
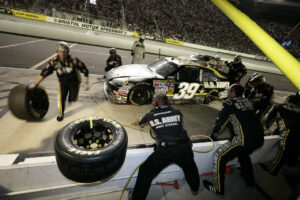
Pit stops on a race track must take no longer than 10 seconds. As the cars travel at 200 miles per hour, every second in the pit counts. Each second represents over 200 feet on the race track! Therefore, it is imperative that the pit team is as efficient as possible; the margin for victory is literally in inches.
How the pit stop works
Each job is identified and assigned to someone. Everyone knows their job and is focused on the ultimate goal of finishing the stop as quickly as possible. All of the parts and materials are pre-staged before the pit sop even begins (i.e. tires, tools, etc.). Teams have eliminated the use of tools whenever possible like in the use of tear away windshields, but do use tools where they cannot be eliminated. And finally, pit stop teams continuously train, measure, and perfect their processes. The same sort of diligence, training, and measuring is applied to factories.
References:
Business Insider (2021, June 24). How IndyCar pit crews are trained [Video]. YouTube. https://www.youtube.com/watch?v=Ba9S_0E9Bf4
Engaged Mobile (2014, May 7). Engaged Mobile presents “The art of the Verizon IndyCar pit stop” with RLL Racing using Google Glass [Video]. YouTube. https://www.youtube.com/watch?v=YZebWF40DKI
Dennis, P. (2016). Lean production simplified : a plain-language guide to the world’s most powerful production system (Third). CRC Press, Taylor & Francis Group.
Diaz-Reza, J., Garcia-Alcaraz, J., Mendoza-Rong, J., Martinez-Loya, V., Macias, E., & Blanco-Fernandez, J. (2017). Interrelations among SMED stages: A causal model. Complexity. https://doi.org/10.1155/2017/5912940
Indrawati, S., Pratiwi, M., Sunaryo, & Azzam, A. (2018). The effectiveness of single minute exchange of dies for lean changeover process in printing industry. MATEC Web of Conferences, 154 https://doi.org/10.1051/matecconf/201815401064
“SMED (Single-Minute Exchange of Die).” 2021. Lean Production. https://www.leanproduction.com/smed/
Moreira, A. & Pais, G. (2011). Single minute exchange of die. A case study implementation. Journal of Technology Management and Innovation 6(1). http://DOI: https://doi.org/10.4067/S0718-27242011000100011
Trout, J. (2022). SMED: What it is an why it matters. Reliable Plant. https://www.reliableplant.com/Read/14965/smed-quick-changeover-program
Warped Perceptions (2019, July 20). 6 second pit stop in slow motion [Video]. YouTube. https://www.youtube.com/watch?v=GND3c80ZnTQ