Chapter 2: Just-In-Time Production Concepts
Overview
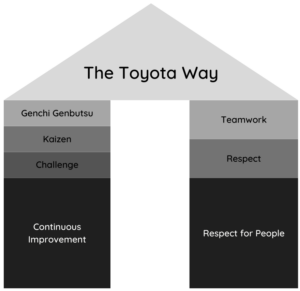
Just-in-time production (JIT) is an inventory management philosophy that reduces inventories to minimum levels. JIT is designed to reduce waste in any form, like that associated with maintaining inventory, but also storage and transport (Saylor, 2019), or wasted time (“Operations Strategy”, 2017). The ideal system would have zero stocked finished goods and WIP, and minimal stocked raw materials. Taiichi Ohno is credited for developing this lean system and for perfecting it within Toyota’s car manufacturing plants in Japan. Related to lean manufacturing, it seeks to reduce or eliminate any part of the manufacturing process that does not add value from the customer’s viewpoint (Saylor, 2019; Rice University). Moreover, it assists organizations to meet their capacity and promotes consistent flow through the manufacturing process (Qureshi et al., 2013). Here are some examples of waste (Saylor, 2019, Qureshi et al., 2013; Siddiqui, 2022)):
Review the series of short videos below to learn what JIT is and it’s connection to Toyota.
Takt Time
Takt time is one of the most important calculations involved with lean manufacturing (Soliman, 2020). Takt time is the average time it takes from the start of production of one unit to the start of the next units production, when they are produced sequentially. Takt time is calculated by taking the time to produce the parts and dived it by the number of parts demanded in that interval. It is also based on customer demand, so if a product cannot be produced using takt time, other strategies will have to be used in order to meet the demand (“Takt Time”, 2022). Because the time must represent the actual customer demand rate, do not adjust times for any slow downs, like you would with other calculations (Soliman, 2020). Learn more about takt production and control from this study: Takt Production Monitoring and Control in Apartment Renovation Projects (Keskiniva et al., 2021)
Here’s an example calculation of Takt Time. Please note that customer demand is expressed in the maximum allowable time per unit:
If there are a total of 10 hours (or 600 minutes) in a shift (gross time), less 60 minutes for lunch, 10 minutes for team briefing, and 10 minutes for basic maintenance checks, then the net Available Time to Work = 600 – 60 – 10 – 10 = 520 minutes (31,200 seconds)
If customer demand was 520 units per day and only one shift was available, then the link would be required to output at a minimum rate of one part per 60 seconds in order to keep up with customer demand.
Formula for calculating takt time:
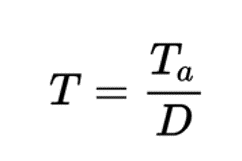
Ways to Meet JIT Goals
Inventory Reduction
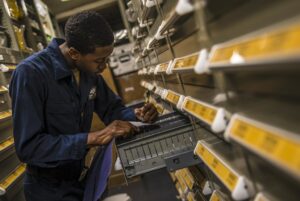
An expansive inventory hides a lot of issues, ranging from equipment problems, bad vendors, low quality, and others. Gradually, by lowering the amount of inventory, weaknesses are revealed and can be updated to be more efficient and effective (Rice University). Reducing inventory requires a few, very reliable vendors to deliver both materials and the inventory within very short time frames, generally in small lots. This reduces costs but it can be challenging to find the right vendors (Franco & Rubha, 2017).
Demand-Pull Production System
The demand-pull system functions in such a way that the work flows to the organization that needs work. JIT also addresses concerns and challenges related to production and waste reduction strategies in order to meet its goals, especially without inventory around to cover weaknesses (Rice University). This systems of one of the tools the Toyota Production System uses to achieve success, the consumer triggers production to meet their requirements at the right time and quantity (Si et al., 2021)
Reduce Lot Sizes
Manufacturing entities that improve their setup can reduce the lot size, increasing competitiveness. (Rice University). Here is an example from the 1980s and 3M, provided by Rice University:
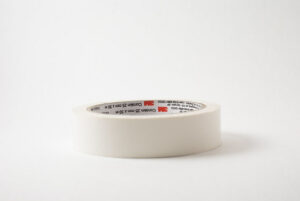
“In the 1980s, the 3M company converted a factory that made a few adhesive products in long production runs into a factory that made over 500 adhesive products in small production runs. To keep unit production costs under control, 3M studied the setups on its coating machines. Since the cost of chemical waste disposal was a major part of the cost of changing over a coating machine to make another product, 3M shortened the length of hoses that needed purging and redesigned the shape of the adhesive solution holding pan on the coating machine to be shallower. 3M also used quick-connect devices, disposable filters, and work teams to speed up setups. The result was that 3M could maintain low unit costs on its coating machines while producing small lots of hundreds of products to meet market demand quickly.”
Plant Loading
This strategy means that companies have the insight to provide the needed products, at the needed moment and place in time. The concepts are building on each other now, reducing inventory to meet exactly to meet demand, and promoting more effective manufacturing processes to hit goals at the right time (Rice University).
Flexible Resources
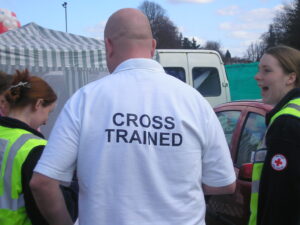
The unknown is something that makes JIT enterprises vulnerable and unfortunately, it cannot be eliminated in all cases. The best strategy to overcome uncertainty is a certain level of flexibility built into the organizational structure. Maybe it is drills that can swap bits easily, so one drill can do the work of 10 drills. Or maybe it is the color application method that can switch from one color to another without changing equipment like hoses or nozzles. This bit of flexibility can improve output and make JIT organizations more productive (Rice University); it does require that the equipment is maintained and functioning properly. Additionally, flexible, cross-trained employees and adaptive environments minimize waste by synchronizing the flow throughout the process (Franco & Rubha, 2017).
Flow Layouts
If the layout of the building is a perfect way to improve flow and productivity. In this situation, manufacturers set up their buildings to have one-way flow of the operation and have respective areas where employees take responsibility and control of their products (Rice University). Generally, this empowers employees to take ownership in their work.
Empowered Employees
Select each of the hot spots below on the graphic to learn more about the effects of empowering employees in the JIT model.
Potential Challenges with JIT
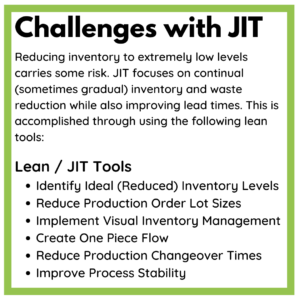
There can be challenges with implementing JIT, beyond the fact that it is a complex system. For example, JIT manufacturing is vulnerable in regards to natural disasters. Because these organizations reduce the amount of on-hand inventory, they do not have stock to spare in the case of tsunami, hurricanes, flood, and other disasters (Qureshi et al., 2013; Siddiqui, 2022). Production is at the mercy of suppliers, so if one thing is off, the rest of the system is delayed (Siddiqui, 2022; Franco & Rubha, 2017), Communication also seems to be a relevant concern in JIT approaches; it is imperative that the communication structure and strategies are conveyed to all of the relevant workers to reliably share information (Qureshi et al., 2013), including maintaining positive relationships with contractors and other entities (Si, 2021).
Learn more about other ideas related to JIT in this study about off-site construction to build productivity and improve performance: A Dynamic Just-In-Time Component Delivery Framework for Off-Site Construction (2021). You can also view this video below as a review of JIT as well as the advantages and disadvantages of this type of manufacturing.
References
Berman, A. (2017, September 29). Just in time by Toyota: The smartest production system in the world [Video]. YouTube. https://www.youtube.com/watch?v=cAUXHJBB5CM
Dennis, P. (2016). Lean production simplified : a plain-language guide to the world’s most powerful production system (Third). CRC Press, Taylor & Francis Group.
EducationLeaves (2022, March 23). Just in time or JIT [Video]. YouTube. https://www.youtube.com/watch?v=9onMrDbDKaM
Franco, C., & Rubha, C. (2017). An overview about JIT (just-in-time) – Inventory management system. International Journal of Research – Granthaalayah, 5(4). doi: https://doi.org/10.5281/zenodo.569368
Learn Transformation (2021, March 5). Just in time in 2021 [Video]. YouTube. https://www.youtube.com/watch?v=Rj4866wTiRc
Keskiniva, K., Saari, A., & Junnonen, J. (2021). Takt production monitoring and control in apartment renovation projects. Buildings, 119(3). https://doi.org/10.3390/buildings11030092
Matlack, A. (2018, October 2). Beyond engagement: What leaders need to know about empowering others. OpenSource. https://opensource.com/open-organization/18/10/understanding-engagement-empowerment
NetSuit (2021, July 9). What is just-in-time inventory management? [Video]. YouTube. https://www.youtube.com/watch?v=zCTmN17ZDek
“Operations Strategy/JIT” (2017). Wikipedia. Retrieved on July 26, 2022 from https://en.wikibooks.org/wiki/Operations_Strategy/JIT
OpsExcellence (2015, February 10). Takt time, cycle time, lead time [Video]. YouTube. https://www.youtube.com/watch?v=isu6MG3v0-s
Qureshi, M., Iftikhar, M., Bhatti, M., Shams, T., & Zaman, K (2013). Critical elements in implementation of just-in-time management: Empirical study of cement industry in Pakistan, 2. https://doi.org/10.1186/2193-1801-2-645
Rice University (n.d.). Operations management: Special topic – Just in time and lean systems. Operations Management. Retrieved January 26, 2022 from https://courses.lumenlearning.com/suny-opmanagement/chapter/6-4-jit-pull-systems/
Saylor Academy (n.d.). The benefits of empowering employees. Principles of Management. Retrieved July 26, 2022 from https://learn.saylor.org/mod/url/view.php?id=9592
Saylor Academy (2019, April 9). Just-in-time and lean systems. Operations Management. Retrieved July 26, 2022 from https://learn.saylor.org/mod/page/view.php?id=9276
Si, T., Li, H., Lei, Z., Liu, H., & Han, S. (2021). A dynamic just-in-time component delivery framework for off-site construction. Advances in Civil Engineering. https://doi.org/10.1155/2021/9953732
Siddiqui, A. (2022). The importance of just in time (JIT) methodology and its advantages in health care quality management business – a scoping review. Biomedical Journal of Scientific and Technical Research, 42(1). DOI: 10.26717/BJSTR.2022.42.006701
Soliman, M. (2020). Takt time, cycle time, one-piece flow, and hejunka. Zenodo. Retrieved on July 29, 2022 from https://zenodo.org/record/4289284#.YuPOXhzMKUl
“Takt Time” (2022). Wikipedia. Retrieved on July 29, 2022 from https://en.wikipedia.org/wiki/Takt_time
producing more than is needed to meet customer demands.
Long wait times for products to be made or customers waiting in a queue
Using transportation to move materials, excessive; or customers have to travel through a building to reach the product.
Example: start up costs
space, deterioration, maintenance, etc.
Example: ineffective work techniques
Waste produced from reworking defective products, using scrap, or to execute warranties.