Chapter 1: Introduction to Lean Manufacturing
Overview
Lean manufacturing is the production method used to reduce production times as well as response times to customers. Lean manufacturing adopts a method of manufacturing according to demand, but also attempts to reduce waste. Generally, this process will include marketing and customer service personnel who can identify the wants of its customer base and report back to the manufacturer (Kulkarni et al., 2021; Gil-Vilda et al., 2021). The transition from a traditional company to a lean company is complex and needs to be carefully organized in order to maximize income, reduce costs, and to improve productivity (Cimermancic et al., 2022; Pearce & Pons, 2013). Review the slides and video below to learn more about the history of manufacturing and the shift to lean manufacturing. Use the double pointed arrow in the lower right corner to expand slides to full screen.
Lean Operations
Lean refers to an item being as slim as possible, like there is no fat, no waste. The fat or waste in a company would be excessive or inefficient operations, but lean manufacturing has no waste (Boardman; Kulkari et al., 2021). There are eight kinds of waste (or ) in some models. They are: transport, inventory, motion, waiting, over-production, over-processing, defects, and skills. Lean manufacturing focuses on the five following concepts as a way to reduce all of these kinds of waste (Boardman; Brown, 2020; de Bucourt et al., 2011).
Value and Value Stream
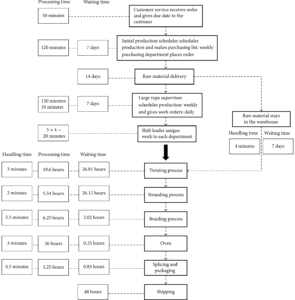
This concept is defined by the customer. The organization must have a clear understanding of what value is for the customer. It is wasteful to create a product that customers do not find value in buying (ASCM, 2022). Data provided by continuous customer feedback is how this concept is defined and constantly adapted to meet the needs of the customer base (Boardman). Consider the surveys provided at the end of receipts to elicit feedback on your shopping experience. This type of feedback is important for an organization to adapt with trends and demands.
To track the value of a product, a value stream map can identify the activities that add value or not, including the processes that are essential and cannot be eliminated. Terms to know are , , and (Boardman). Learn more about value stream mapping from these resources:
- This case study about a steel pipe manufacturer: Using Value Stream Mapping to Eliminate Waste: A Case Study of a Steel Pipe Manufacturer (2021).
- This resource What is a Value Stream Map? (2021) shares the reasons you need value stream mapping and common mistakes that are made in the process.
Please also review this series of six videos that provide clear lessons on how to do Value Steam Mapping.
Flow
Flow is defined is characterized by continuously moving through the manufacturing process without time to pause in storage or in transport. Flow eliminates batches and queues from the system so the product continuously moves without delay. Flow should complement the market demand, to keep the process clean and consistent (Boardman; Saylor). Consistent flow reduces waste caused by starting and stopping the production process (ASCM, 2022).
Flow is increased by eliminating bottlenecks. Consider a business a wide mouth jar and a bottle. When the process is consistent and the flow meeting the needs of demand, there is nothing to slow it down as it exits the facility (or jar, for this example). But, if the company is a bottle, when the flow reaches the neck of the bottle, the flow is delayed. This is where the process is running at the least capacity, slowing the flow of the product to the customer. Eliminating these bottlenecks will improve the flow and reduce waste (Boardman; Virasak).
Pull and Pursuit of Perfection
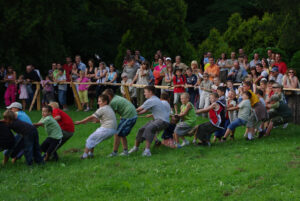
In this lean system, a product is not created until it is asked for by the customer, until it is pulled by the customer rather than pushed by the system. Reduction in lead times to meet the demands of the pull will reduce wasted time spent in storage or transport. These processes are always continuously improving (also known as ), manufacturers encourage internal competition to be more perfect than they were yesterday (Kulkari et al., 2021; ASCM, 2022). Many companies implement continuous improvement practices to promote competition within their field, in addition to the internal structure. (Huang et al 2022).
References
Association for Supply Chain Management (2022). Lean manufacturing. ASCM. https://www.ascm.org/lp/lean-manufacturing/?utm_source=google&utm_medium=cpc&utm_campaign=nb+all+dsa&gclid=Cj0KCQjw_viWBhD8ARIsAH1mCd6TDIbJbsrqPJOcoFTpiRTZGokHunL1RRSCWUyNjMrP0ezCT7vWbx4aAq3oEALw_wcB
Boardman, B. (n.d.). Introduction to industrial engineering. UTA. Retrieved on July 26, 2022 from https://uta.pressbooks.pub/industrialengineeringintro/chapter/lean-operations/
Brown, M. (2020). SC2020: Toyota production system & supply chain. MIT Global Scale Network. https://dspace.mit.edu/bitstream/handle/1721.1/101917/2005_1_Brown.pdf?sequence=1&isAllowed=y
Cimermancic, D., Kusar, J., & Berlec, T. (2022). A procedure for the introduction of leanness into a company. Central European Journal of Operations Research, 30. https://doi.org/10.1007/s10100-020-00732-3
Corbett, P., Janssen, V., Lund, J., Pfannestiel, T., Vickery, P., & Waskiewics, S. (n.d.) U.S. History. OpenStax. Retrieved July 25, 2022 from https://courses.lumenlearning.com/ushistory1os2xmaster/chapter/early-industrialization-in-the-northeast/
Dennis, P. (2016). Lean production simplified : a plain-language guide to the world’s most powerful production system (Third). CRC Press, Taylor & Francis Group.
de Bucourt, M., Busse, R., Güttler, F., Wintzer, C., Collettini, F., Kloeters, C., Hamm, B., & Teichgraber, U. (2011) Lean manufacturing and Toyota Production System terminology applied to the procurement of vascular stents in interventional radiology. Insights Imaging 2, 415–423 https://doi.org/10.1007/s13244-011-0097-0
Engineeers Academy (2021, August 27). An introduction to lean manufacturing: Work and manufacturing processes [Video]. YouTube. https://www.youtube.com/watch?v=RsQvfdwCiC4
FlowPlus (2021, February 5). #4 free lean six sigma green belt: The history of lean manufacturing [Video]. YouTube. https://www.youtube.com/watch?v=ejhYJ6sMMSY
Gil-Vilda, F., Yague-Fabra, J., & Sunyer, A. (2021). From lean production to lean 4.0: A systematic literature review with historical perspective. Applied Sciences, 11(21). https://doi.org/10.3390/app112110318
Girdler, A. (2020, February 5). How to value stream map [Video]. YouTube. https://www.youtube.com/watch?v=7wD7R6x3Pv4
Kulkarni, S., Nagare, R., Nagare, D., & Aware, P. (2021). Toyota production system – Maximizing production efficiency by waste elimination. International Advanced Research Journal in Science, Engineering, and Technology, 8(4). DOI: 10.17148/IARJSET.2021.8448
“Lean Manufacturing” (2022, July 4). Wikipedia. https://en.wikipedia.org/wiki/Lean_manufacturing
LeanVlog (2017, November 26). How to do value stream mapping [Video]. YouTube. https://www.youtube.com/watch?v=fkk0hkunfcE
LeanVlog (2018, March 17). How to do value stream mapping: Customer demand [Video]. YouTube. https://www.youtube.com/watch?v=8gvaK6ihETE
LeanVlog (2018, June 16). How to do value stream mapping: The process box [Video]. YouTube. https://www.youtube.com/watch?v=2rhzsq_W2wo
LeanVlog (2018, November 18). How to do value stream mapping: The material flow [Video]. YouTube. https://www.youtube.com/watch?v=WfwS26vHeVI
LeanVlog (2019, May 25). How to do value stream mapping: The information flow [Video]. YouTube. https://www.youtube.com/watch?v=fNt-u1LrFmw
LeanVlog (2019, August 31). How to do value stream mapping: The time ladder [Video]. YouTube. https://www.youtube.com/watch?v=tTCGR9mXQLI
“Muda (Japanese term)”. (2022, June 22). Wikipedia. https://en.wikipedia.org/wiki/Muda_(Japanese_term)
Pearce, A. & Pons, D. (2013). Implementing lean practices: Managing the transformation risks. Journal of Industrial Engineering. https://doi.org/10.1155/2013/790291
Salwin, M., Jacyna-Golda, I., Banka, M., Varanchuk, D., & Gavina, A. (2021). Using value stream mapping to eliminate waste: A case study of a steel pipe manufacturer. Energies, 14(12). https://doi.org/10.3390/en14123527
Saylor Academy (n.d.). Operations management. NSCC. Retrieved on July 26, 2022 from https://pressbooks.nscc.ca/operationsmanagement2/chapter/6-1-lean-manufacturing/
Virasak, L (n.d.) Manufacturing processes 4-5. Open Oregon. Retrieved on July 26, 2022 from https://openoregon.pressbooks.pub/manufacturingprocesses45/chapter/chapter-7-lean-manufacturing/
Yuvamitra, K., Lee, J., & Dong, K. (2017). Value stream mapping of rope manufacturing: A case study. International Journal of Manufacturing Engineering. https://doi.org/10.1155/2017/8674187
Japanese word meaning waste. It is the key concept in lean manufacturing, closely associate with Toyota Production System.
something that creates value and the customer can recognize that value.
items that do not add value, within the customer range of perception, and should (could) be eliminated.
regulatory policies or company-wide policies that cannot be eliminated from the system, but also do not add value to the product.
continuous improvement for all from top management all the way down to the workers.